Creating the ideal storage and fulfillment solution for your warehouse requires strategic planning, efficient design, and the right equipment to maximize space and productivity.
If you aim to increase storage or modify your existing setup, certain factors are essential when designing your warehouse layout and pallet rack system. A brief overview of the process and examining storage rack options will guide you toward the most effective solution for your specific storage and fulfillment requirements.
Space Available
The physical size of your warehouse will dictate rack heights and depths, worker movement patterns and operation space for material handling equipment. Expert storage system designers will consider all the building parameters (such as square footage, ceiling height, obstructions, dock door placement, etc.) to optimize your ideal storage efficiency.
Product Profile
The next step in your design is a comprehensive inventory review. The specifications of the items you need to store—their size, shape, weight, and pallet type—will help determine your ideal storage options and the type of material (for instance, roll-formed or structural steel) you’ll choose for your pallet rack frames and beams.
Inventory Movement
You also need to assess your inventory requirements, including:
- Inventory Rotation: FIFO or LIFO product rotation will dictate specific industrial ideal storage rack options.
- Inventory Throughput: You need to consider how much of your inventory is static vs. dynamic and how fast your inventory moves. Do you need to account for changes in inventory or seasonality? What is the growth potential you wish to plan for?
- Picking Accessibility: Which items and how many of each are picked as a full pallet, and how many are broken into cases for an entire case or individual item picking?
- Equipped with the above information, you can explore storage racking options to identify the best solutions for your needs.
Equipped with the above information, you can explore ideal storage racking options to identify the best solutions for your needs.
The choices: Industrial Storage Rack Systems
- Selective pallet rack – single deep, 100% selectivity (2-deep is also an option). Best for high-throughput, low SKU density.
- Push-back pallet rack – LIFO storage, typically 3-4 deep but can be deeper. High-density solution requiring specialized equipment for pallet positions above 20′.
- Drive-in/drive-through pallet rack – LIFO storage, high-density, low SKU option, 10+ deep. It is best used for large quantities of similar products stored in a single pallet position.
- Pallet flow storage rack – Gravity flow FIFO storage, high-density, 2-10 deep. Best for inventory rotation of perishable goods.
- Cantilever rack – Adjustable arms on uprights to hold awkward-sized, long, or heavy material that standard pallet storage cannot accommodate, e.g., reels, furniture, and tires.
- Carton flow systems – Gravity flow FIFO storage for full & split-case picking.
- Pick modules – combine pallet and carton storage in a multi-level storage system utilizing two or more racking options for productive order picking.
The Specifics: Safety Features and Accessories
No industrial ideal storage rack system design is complete without safety features – guide rails, upright and row protectors, sprinkler systems, and so on are critical features to include in your completed project. Other items like dock accessories, interior and exterior doors, mezzanines, and stairs will also be added to meet all OSHA requirements and overall efficiency demands.
Trimet Storage Solutions is a full-service company offering expert support from the initial design process to installation and beyond.
Contact us today for a free consultation and discuss your material handling challenges.
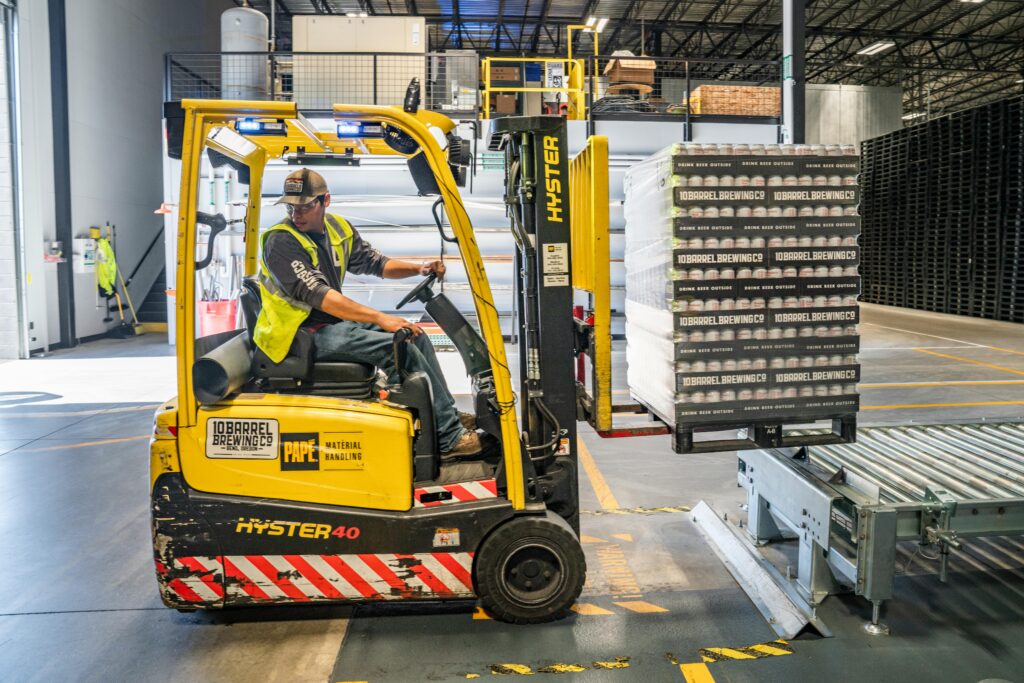