When your warehouse starts feeling overcrowded, it’s easy to assume that any high-density racking system will fix the problem. After all, more pallets in less space sounds like the obvious solution. But the truth is, not every “space-saving” approach is created equal, and choosing the wrong one can create more headaches than it solves.
If you’re exploring ways to expand capacity, you’ve probably come across Drive-In Racking and Very Narrow Aisle (VNA) Racking. On the surface, both promise to boost storage density, but that’s where the similarities end. In practice, these two systems represent fundamentally different strategies: Drive-In Racking trades selectivity for maximum density, while VNA Racking leverages specialized equipment to maintain full pallet access without sacrificing valuable floor space.
In this guide, we’ll walk you through how each system works, the advantages and trade-offs to consider, and how to decide which approach best supports your operation and inventory profile.
What is Drive-In Racking?
Drive-In Racking is a high-density storage system that helps you maximize warehouse space by eliminating most aisles. Instead of accessing pallets from the front of the racks, forklifts drive directly into the structure itself to load and retrieve pallets.
This design makes Drive-In Racking ideal for storing large quantities of the same product, especially when you don’t need frequent access to every pallet. Because pallets are loaded and removed from a single entry point, the system follows a Last In, First Out (LIFO) inventory flow—meaning the last pallet placed in the lane is the first one removed.
Key Features
- High Storage Density: Store up to 75% more pallets compared to standard selective racking by reducing aisle space.
- LIFO Inventory Management: Perfect for products that don’t require strict rotation or have a longer shelf life.
- Single Entry/Exit Per Lane: Each bay has one access point, simplifying loading patterns.
- Rail-Based Support: Pallets rest on rails rather than beams, allowing forklifts to enter each lane.
- Conventional Equipment: No special forklifts required—standard lift trucks can operate in the system.
When to Use Drive-In Racking
Drive-In Racking is a smart choice when:
You handle large volumes of the same SKU.
Inventory moves quickly in batches.
Space utilization matters more than having immediate access to every pallet.
You want to avoid the cost and training requirements of specialized lift equipment.
Typical Applications
Many industries rely on Drive-In Racking to optimize space, including:
- Cold Storage and Freezers: Where maximizing cubic space is critical and product rotation is less frequent.
- Food and Beverage: For storing uniform pallet loads with high turnover.
- Manufacturing: When bulk components or finished goods are stored together.
What is VNA Racking?
Very Narrow Aisle (VNA) Racking is a high-density storage system that helps you maximize warehouse capacity without giving up direct access to every pallet.
Unlike other dense storage solutions that sacrifice selectivity, VNA racking combines tight aisle spacing with 100% selectivity, so you can retrieve any pallet at any time.
To achieve this, the aisles are narrowed—sometimes to as little as 1.6 meters (about 5–6 feet)—which significantly increases the number of rack rows you can fit in the same footprint. Because of these reduced aisle widths, VNA systems require specialized lift equipment, such as turret trucks or articulated forklifts, designed to maneuver safely and efficiently in confined spaces.
Key Features
- High Selectivity: Every pallet remains fully accessible at all times, making inventory management simple and precise.
- Greater Storage Capacity: Narrow aisles allow you to install more rack columns, increasing the total number of pallet positions.
- Specialized Equipment: VNA systems require purpose-built trucks with rotating forks or operator cabins that elevate with the load.
- Efficient Use of Vertical Space: VNA racking is especially effective in warehouses with high ceilings, often reaching heights of 28 feet or more.
- Improved Inventory Control: Ideal for operations with a high number of SKUs and frequent picking requirements.
When to Use VNA Racking
VNA Racking is an excellent choice if your operation:
Manages a wide variety of SKUs that require fast, direct access.
Needs to maximize storage capacity without compromising selectivity.
Operates in a warehouse with high ceilings and limited floor space.
Is prepared to invest in specialized lift equipment and operator training.
Requires precise inventory tracking and efficient order fulfillment.
Typical Applications
VNA racking is commonly used in:
Third-Party Logistics (3PL) warehouses
Retail distribution centers
Pharmaceutical and food-grade facilities
E-commerce fulfillment operations
Any business with high SKU counts and fast-moving inventory can benefit from the balance of density and selectivity that VNA racking offers.
Advantages of VNA Racking
- Maximum Space Utilization: From floor to ceiling, every cubic meter is optimized.
- Direct Access to All Pallets: No need to move other pallets to reach what you need.
- Lower Operational Costs: More efficient picking and storage reduce labor and equipment expenses over time.
- Better Inventory Accuracy: Easier to track and control products compared to block stacking or drive-in systems.
Comparison
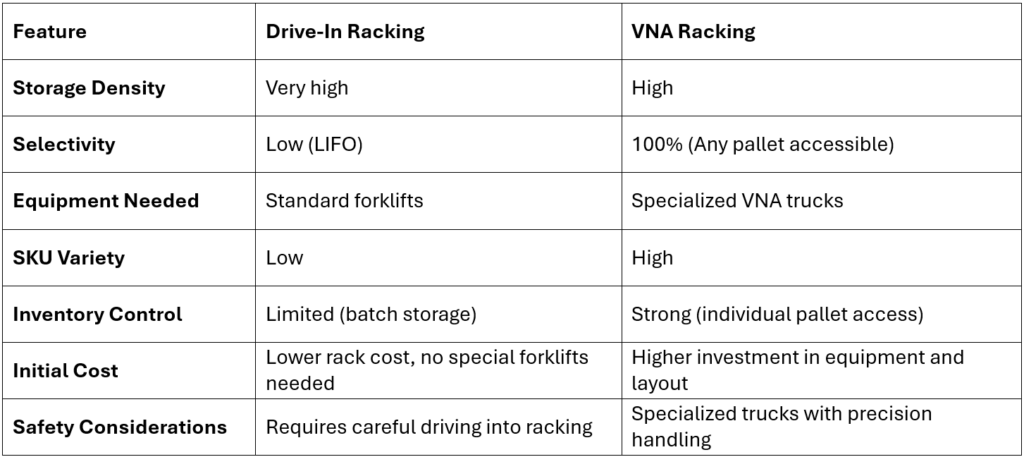
How to Choose the Right System
Selecting the right racking system is more than just a question of space—it’s about aligning your storage method with your inventory profile, operational goals, and long-term plans.
Below are clear considerations to help you decide which approach fits your warehouse best:
Consider Drive-In Racking if:
Your operation handles large volumes of identical products that can be stored in batches.
You need the maximum possible storage density while keeping upfront investment lower.
Your inventory can be managed with a Last In, First Out (LIFO) system, without strict rotation requirements.
You prefer to use standard forklifts rather than investing in specialized handling equipment.
Consider VNA Racking if:
You manage a wide range of SKUs requiring frequent, direct access to individual pallets.
You are prepared to invest in specialized VNA trucks and comprehensive operator training.
Your priority is to maximize storage capacity while maintaining 100% selectivity.
You expect continued growth and need a flexible system that supports high-density storage with precise inventory control.
Safety Trade-Offs to Consider
While both systems are proven solutions, each comes with specific safety considerations:
Drive-In Racking:
Requires forklift operators to drive into rack lanes, which increases the risk of rack impact or damage.
Proper driver training, speed limits, and reinforced rack protections (e.g., column guards) are essential to reduce the chance of accidents.
Limited visibility inside deep lanes can contribute to pallet misplacement or structural damage over time.
VNA Racking:
Narrow aisle spaces demand highly skilled operators and careful maneuvering of specialized equipment.
Because of the height and tight clearances, there is a greater need for safety protocols, including aisle guidance systems, floor flatness standards, and operator certification.
While VNA systems can improve overall safety with better visibility and guided truck navigation, any lapse in training or equipment maintenance can lead to more severe incidents due to the height of loads.
To ensure you select the right system for your operation, consider the following:
How many SKUs do we handle on a regular basis?
Do we need FIFO inventory rotation, or is LIFO acceptable?
Are we prepared to invest in and maintain specialized VNA equipment?
What training will our operators need to safely use the system?
How fast is our business growing, and what will our storage requirements look like in the next 5–10 years?
What safety measures and operational protocols will each system require?
By carefully evaluating your inventory profile, operational constraints, and safety priorities, you can choose the racking system that will support your business efficiently—both today and well into the future.
Ready to Design the Perfect Warehouse Layout?
Whether you’re considering Drive-In Racking, VNA Racking, or exploring other options, our team is here to help you find the right fit for your operation.
Let’s talk about your goals, your space, and how we can make your warehouse work smarter.
Get in touch for a free consultation and a personalized layout analysis.