Pallet Racking is the most common form of warehouse racking systems. Pallet racks are engineered to store palletized materials and products in horizontal rows with multiple levels. The benefits are simple enough: why spend more money to add square feet to a warehouse when you could be utilizing wasted vertical space?
There are many different styles and manufacturers of pallet racking, but all of these share the same goal of increasing storage density by storing pallets off of the ground and utilizing vertical space.
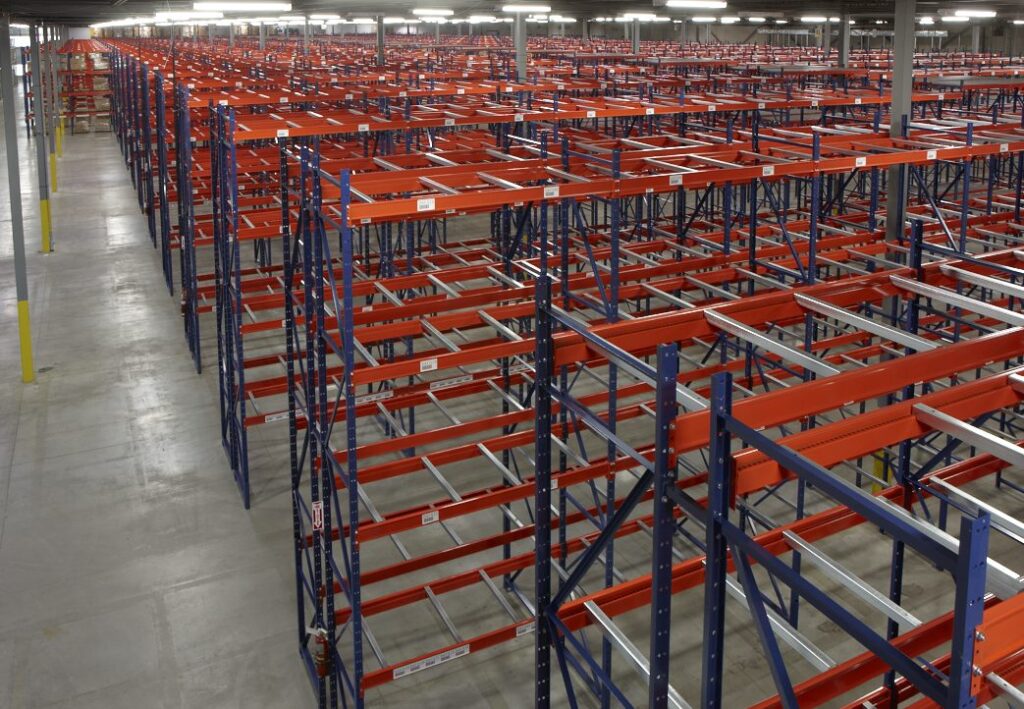
Selective Pallet Rack
Selective pallet racking is very cost-effective, providing high capacity storage and easy access to all pallets.
The name “selective” defines the system quite well, as you can unload any pallet from the system without having to move any other pallets. In this aspect, selective pallet rack offers operators the most flexible storage option.
It is ideal for businesses that have many different products that go to a lot of different places, where orders are complex and involve a mix of different SKUs. Simple to install, selective pallet racking is infinitely adjustable and easy to customize.
Selective pallet racking is serviced by conventional forklift trucks in wider aisle of 10’ to 12’, Reach trucks in 8’ – 10’ aisle, or VNA (Very Narrow Aisle) trucks in 6’ aisles.
Advantages of Selective Pallet Racks:
Direct access to each pallet
Cost-effective – the least expensive rack option available on the market
Versatility –setups are highly customizable and easy to adjust as demands shift.
Ease of installation – pallet rack beams simply lock into frames, and are then secured in place with safety clips
Strength – selective pallet rack is sturdy enough to handle even the most heavy-duty loads
Easy to reconfigure – for increased storage density or a more efficient warehouse layout
Reduced handling time –forklift operators can quickly and easily load or unload pallets from selective racks
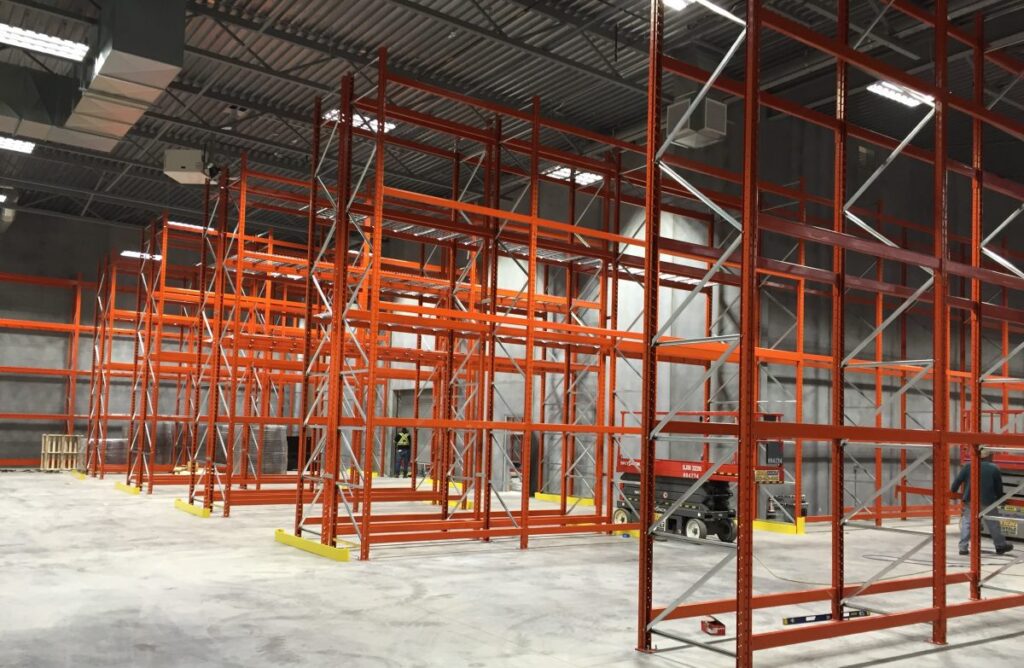
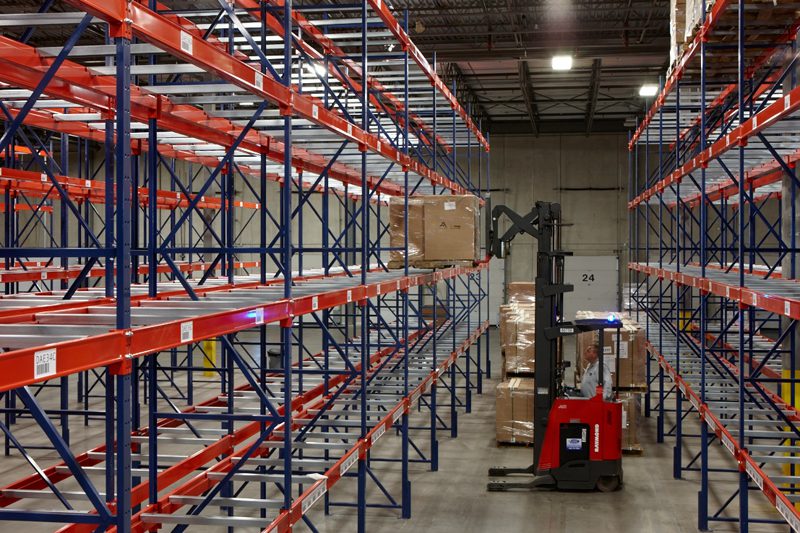
Double Deep Racking
Double-deep pallet racks are created by placing one row of selective pallet racking directly behind another, creating a double deep row, accessed from a single aisle. Double-deep pallet racking systems are utilized in conjunction with Reach trucksor conventional forklift trucks with a pair of extensionto access the rear pallets.
Double-deep pallet racking increases the productive use of floor space at a low initial cost, thereby providing good selectivity and improved density. Double-deep racks are ideal for high throughput operations and offer efficient use of available storage space.


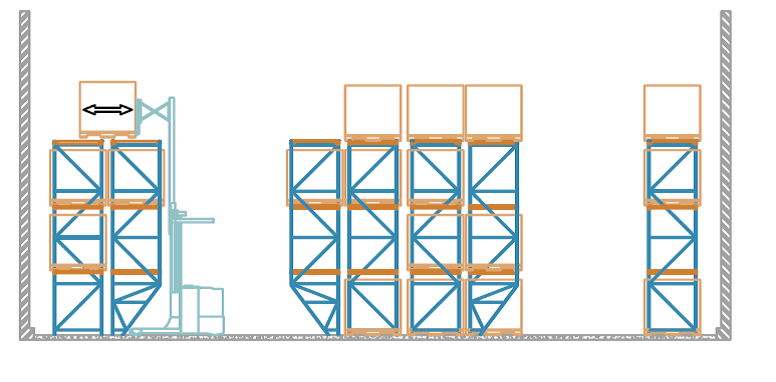
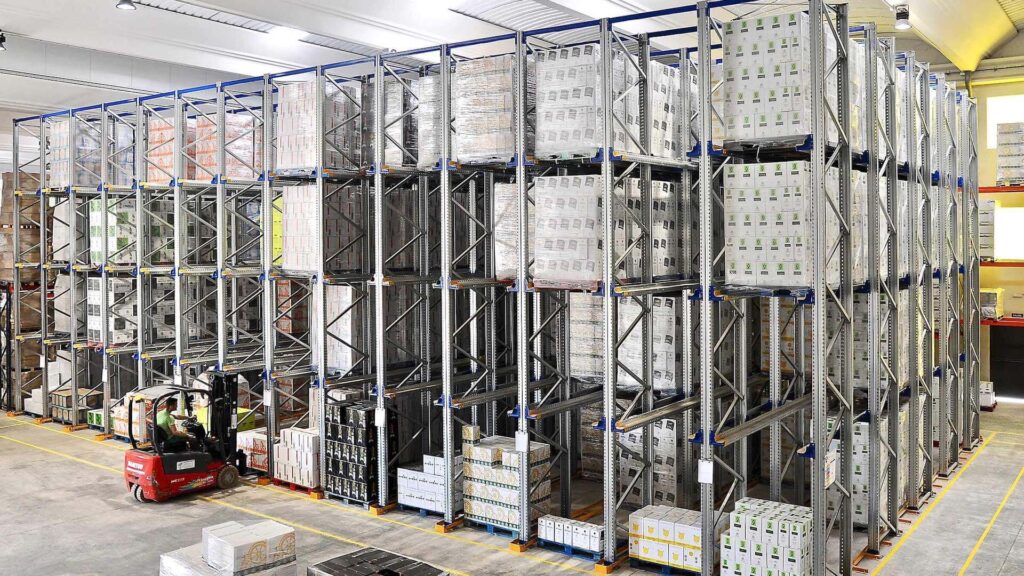
Drive-in Rack
A Drive-In Racking System is a high-density storage solution designed to maximize warehouse space by minimizing aisles and allowing forklifts to drive directly into the racking structure. It is ideal for storing large quantities of the same product (LIFO—Last In, First Out system).
Key Features:
Uses a single entry/exit point per bay.
Forklifts drive into the rack to load/unload pallets.
Pallets are stored on rails, eliminating the need for cross beams.
Best for bulk storage with low SKU variety.
Drive-In vs. Drive-Through Racking:
Drive-In: Single access point (LIFO).
Drive-Through: Two access points, allowing FIFO (First In, First Out).
Best For:
Cold storage (freezers).
High-turnover products.
Industries like food, beverage, and manufacturing.
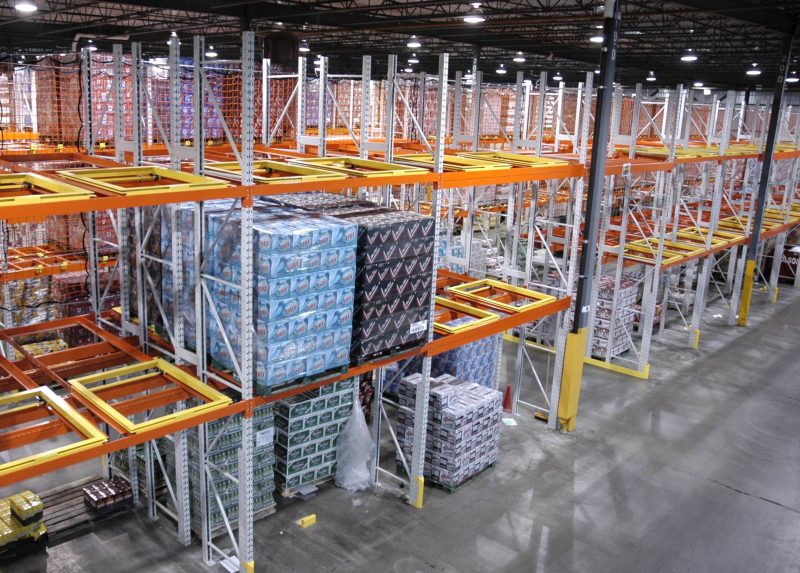
Push-back Racking
Push-back racking is an ideal way to make optimal use of your warehouse floor without having to slow product rotation or increase handling time. When compared to Selective racks, a Push-back racking can offer up to 90% more pallet space by creating a high density storage of max. 6 pallet-deep per lane.
Push-back racking systems are designed to store pallets on wheeled carts that rest on rails. These systems utilize the force of gravity, and so the rails are slightly tilted towards the loading /unloading end of the rack. This enables forklift operators to load pallets onto the carts, as well as push them back as the next pallet is loaded.
Advantages of Push Back Rack Systems:
- Offer much better use of available warehouse floor
- Allows storage of more SKU’s
Labor savings – forklift drivers do not have to remove blocking pallets - Enjoy more storage rack area by eliminating aisles
- Easy & fast loading and unloading of pallets
- Each lane is LIFO, but FIFO can easily be achieved with proper design
Large, coated wheels allow carts to roll smoothly - Very low-maintenance, sealed bearings
Customizable pallet carts, usually color-coded - Low profile cart stack offers max storage height
- Forklifts never have to enter the rack, preventing rack damage
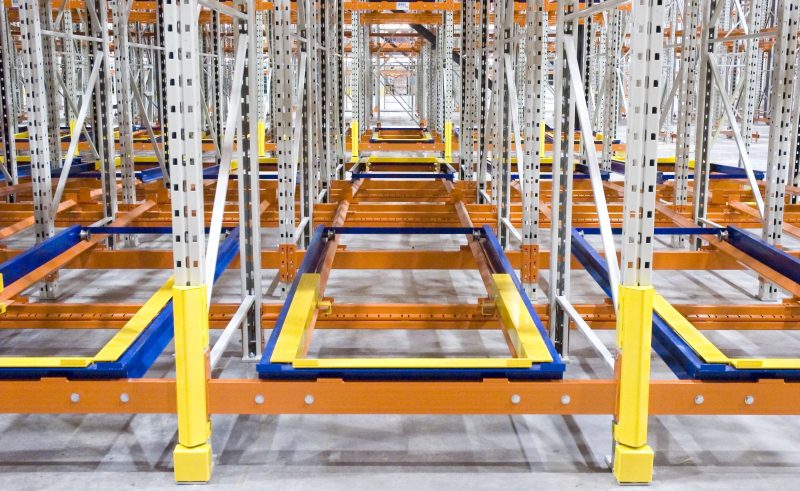
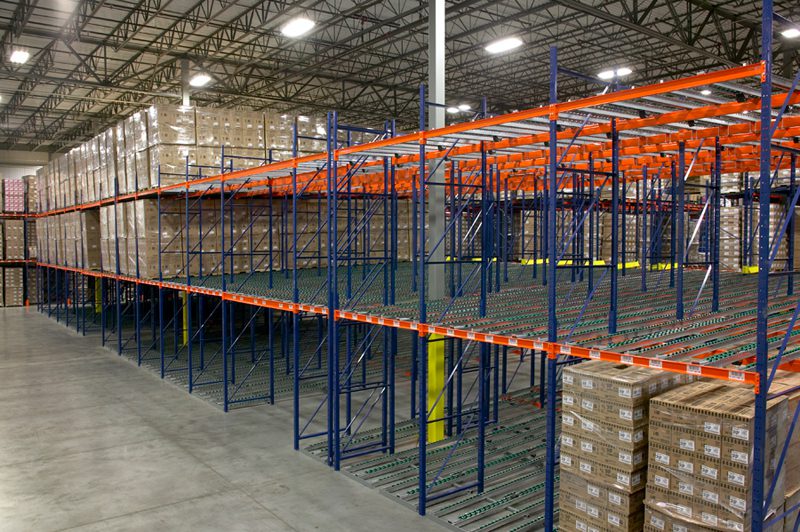
Pallet Flow Racking
Pallet-flow racking, also known as “gravity flow,” is a FIFO (first in, first out) dynamic storage system. The system makes it possible to achieve high density storage (up to 20 pallets per lane) while maintaining product handling efficiency. In comparison to Selective racking, Pallet-flow system eliminates many un-necessary aisles resulting a much better use of warehouse floor space and significant decrease on warehouse operational cost.
In Pallet-flow racking, pallets are first placed onto rollers in loading side, upon which they easily flow towards the dischargeend of the rack system. Once they’ve glided to the front of the system, the pallets rest on pallet stops until they’re unloaded from the pick face. As pallets are removed or unloaded from the system, each of the pallets that were behind them “flow” into the next position via gravity. Pallet speed is controlled by the type of rollers and brakes engineered into the system.
Advantages of Pallet Flow:
- Space-saving, high density storage
- Customized, tailor-made design and layout
- Dynamic “flowing” storage
- Fast, immediate access to every product in each lane
- Versatile, well-suited to refrigerator or freezer storage applications
- Practical and efficient
- Time-saving — only one input and one output aisle
- Minimal maintenance; reliable system
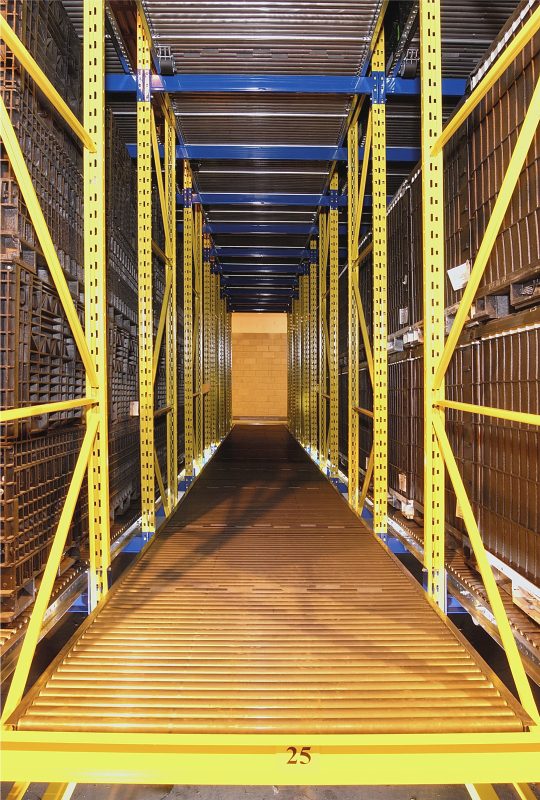
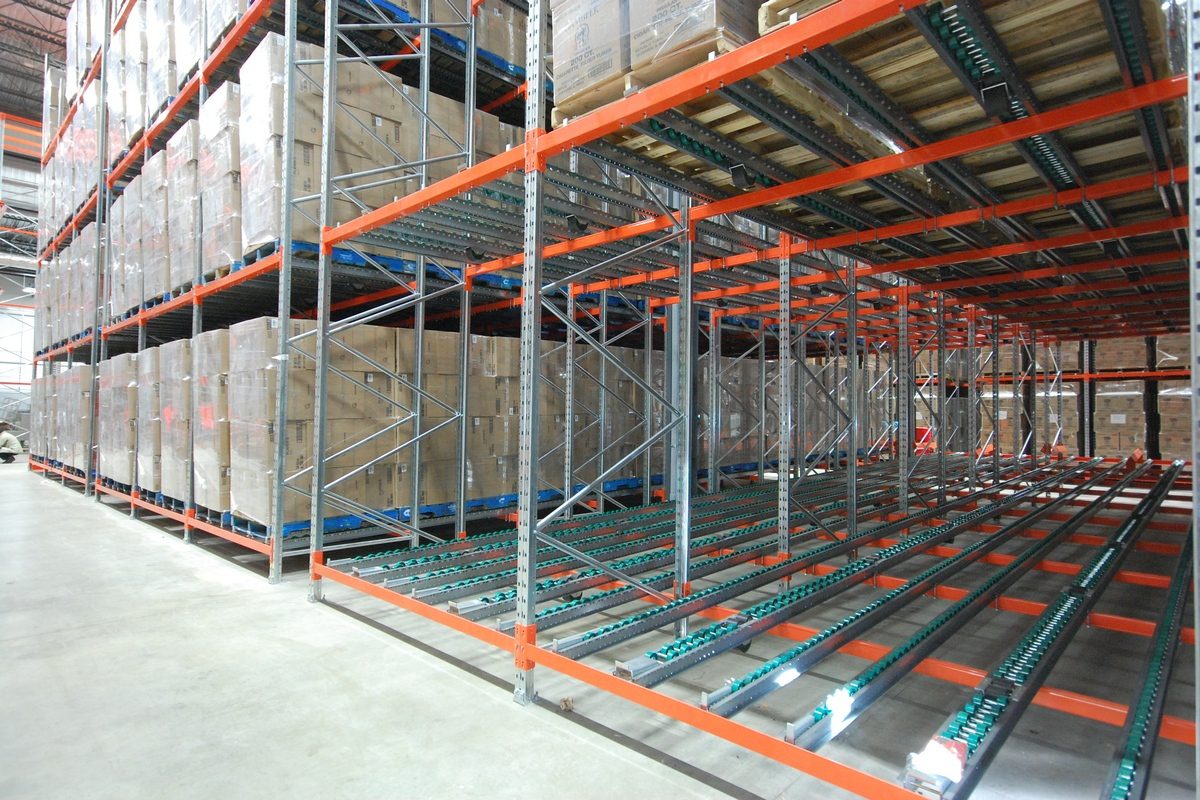
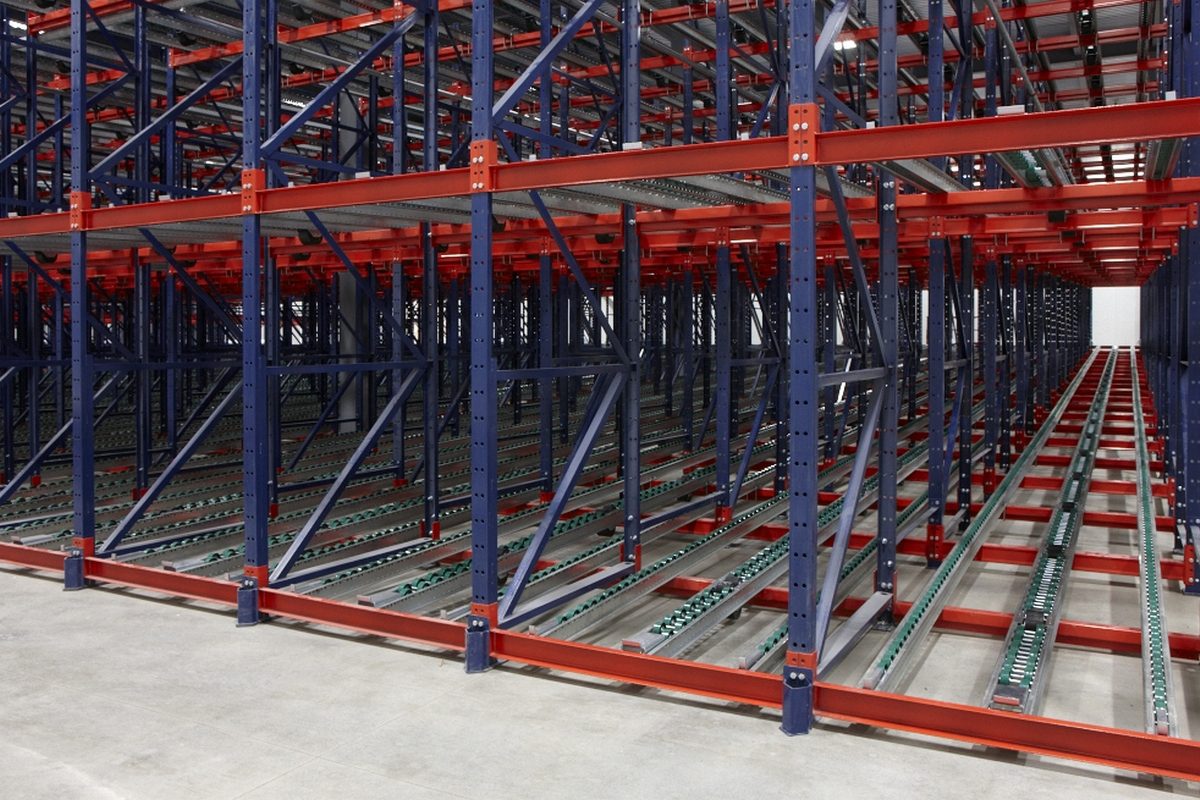
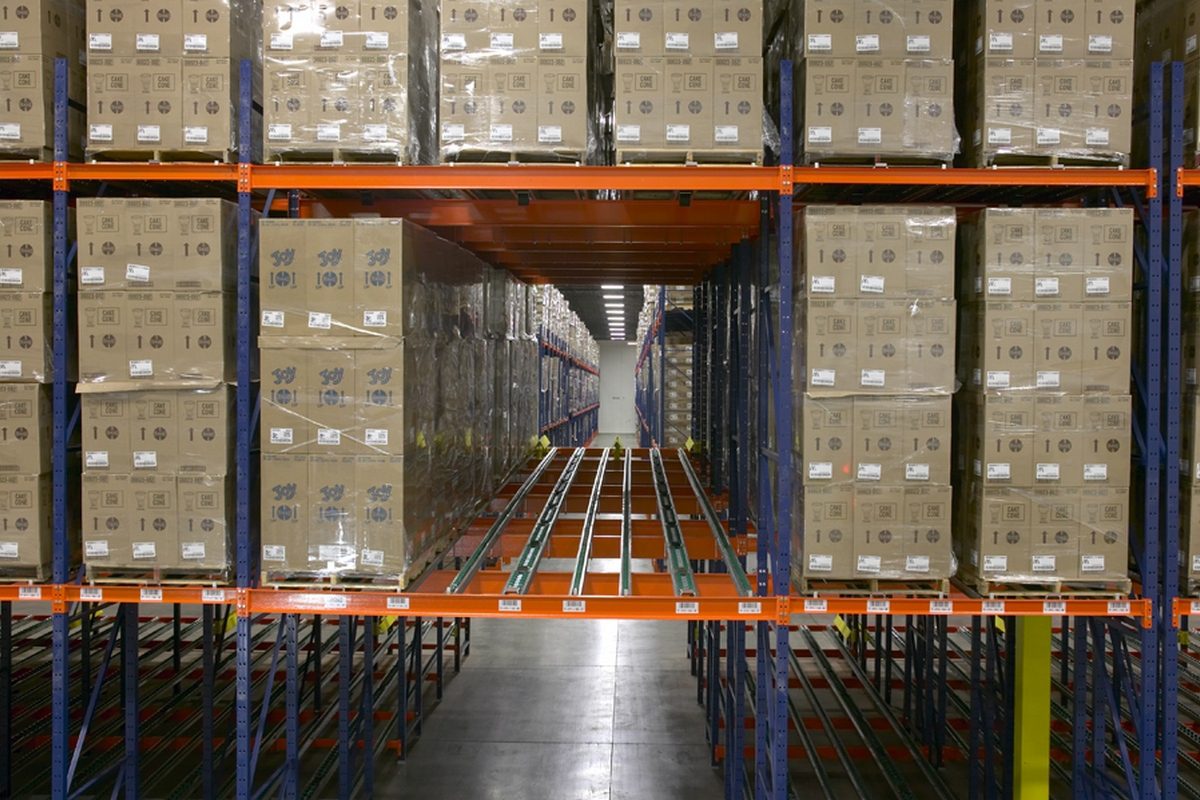
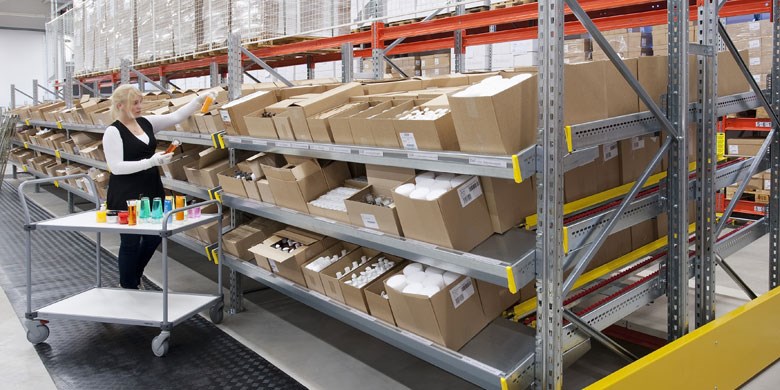
Carton Flow Racking
In use with pallet racking, Carton-flow racks provide an ideal strategy for incorporating case picking with storage of product that picks by the layer from full pallets. The system can be custom engineered to compliment the order filling traffic flow.
With a First-In/First-Out product rotation, carton flow storage racking is commonly found in warehouses with high volume order picking. These gravity driven systems are loaded from the back side and the product (boxes or cartons) flow to the front of the rack system for pick and packing. These products typically include split case and piece picking products such as foods, small parts or small boxes.
Advantages of Carton Flow:
- First in, first out order picking
- Less floor space used
- Lower labor costs
- Less product damage
- Better inventory control
- Can be used in existing pallet rack applications
- Labor time reduction
- Easy to re-slot or reconfigure
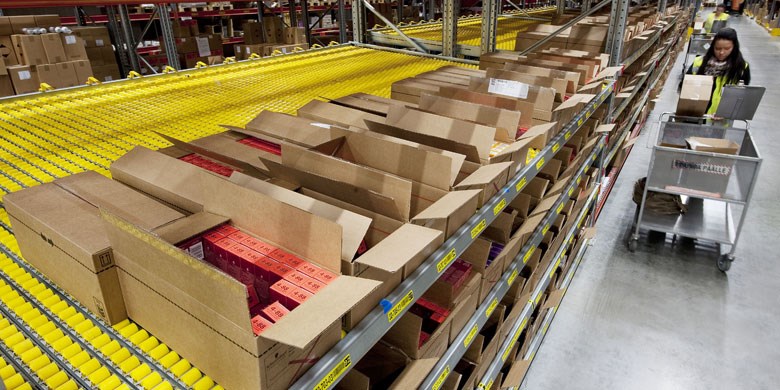
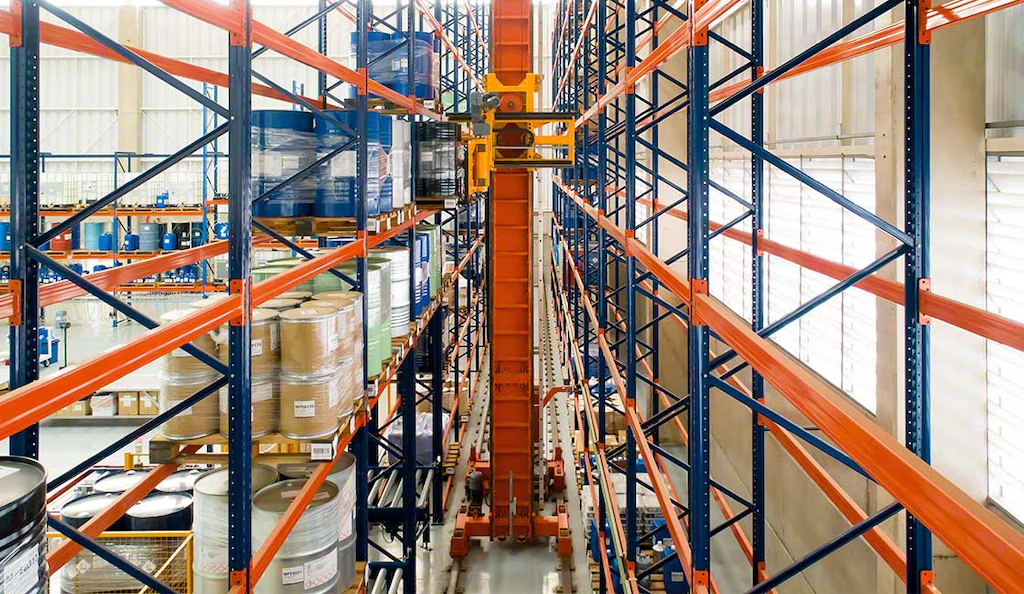
VNA (Very Narrow Aisle)
VNA racking, as the name suggests, makes optimal use of floor to ceiling space in warehouses; resulting in greater storage density. The system designed in warehouse with high vertical space (min. 28’). Same as Selective racking, direct access to every pallet is achieved while the aisles are narrowed down to only 6’ wide. The system is serviced by special forklift trucks called VNW truck; which can come with or without elevated operating cabin.
Advantages of VNA racking:
- Maximum use of the warehouse space; floor to ceiling
- Lower labor and operational cost
- Practical and efficient
- Access to all the pallets
- Better inventory control
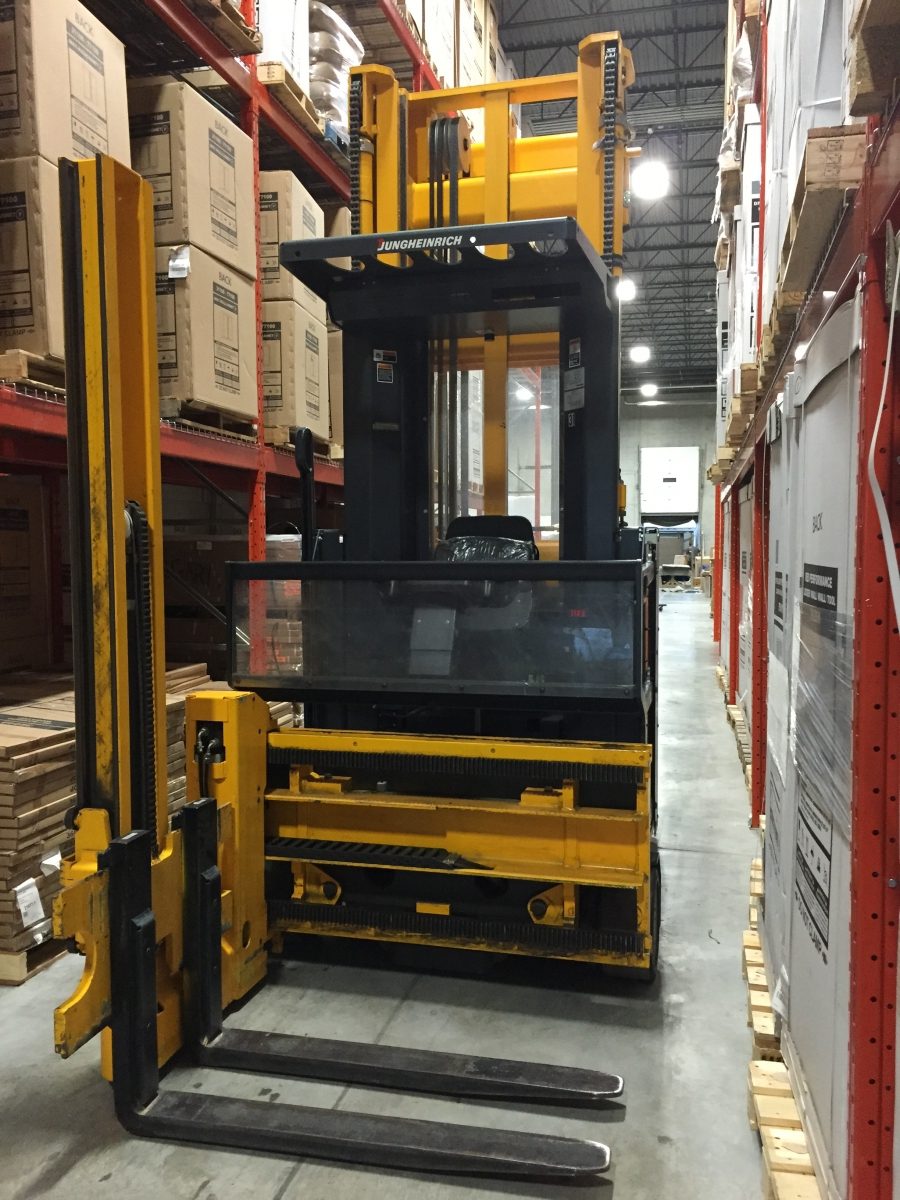
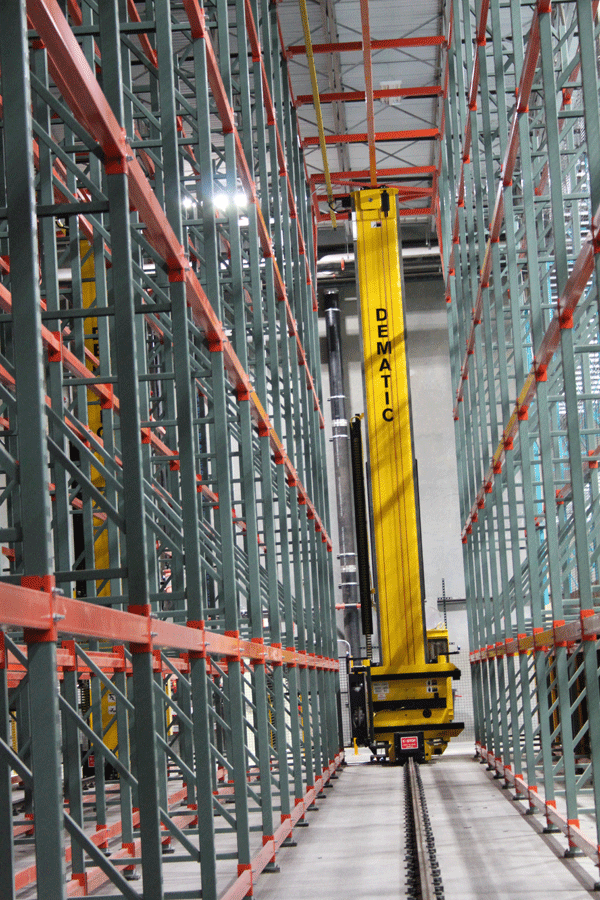
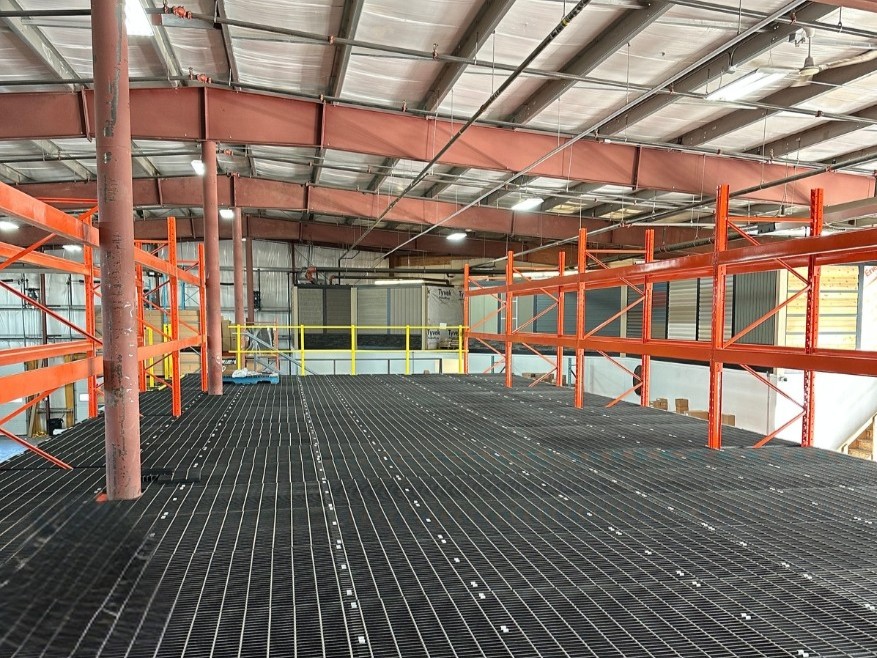
Rack-Supported Platform / Mezzanine
Rack supported platforms represent a sophisticated storage solution where elevated work surfaces are directly integrated into and supported by the warehouse racking structure itself. Unlike traditional mezzanines that require independent structural support, these platforms utilize the vertical posts and horizontal beams of the storage rack system as their primary load-bearing framework. This integration creates multi-level storage and work areas within the same footprint, maximizing vertical space utilization while maintaining direct access to inventory at multiple elevations. The platform decking is engineered to handle both personnel traffic and equipment loads, making it ideal for order picking, quality control stations, and inventory management operations in high-density storage environments.
Advantages:
- Maximized Space Utilization
- Cost-Effective Installation
- Integrated Storage Access
- Flexible Configuration
- Enhanced Workflow Efficiency
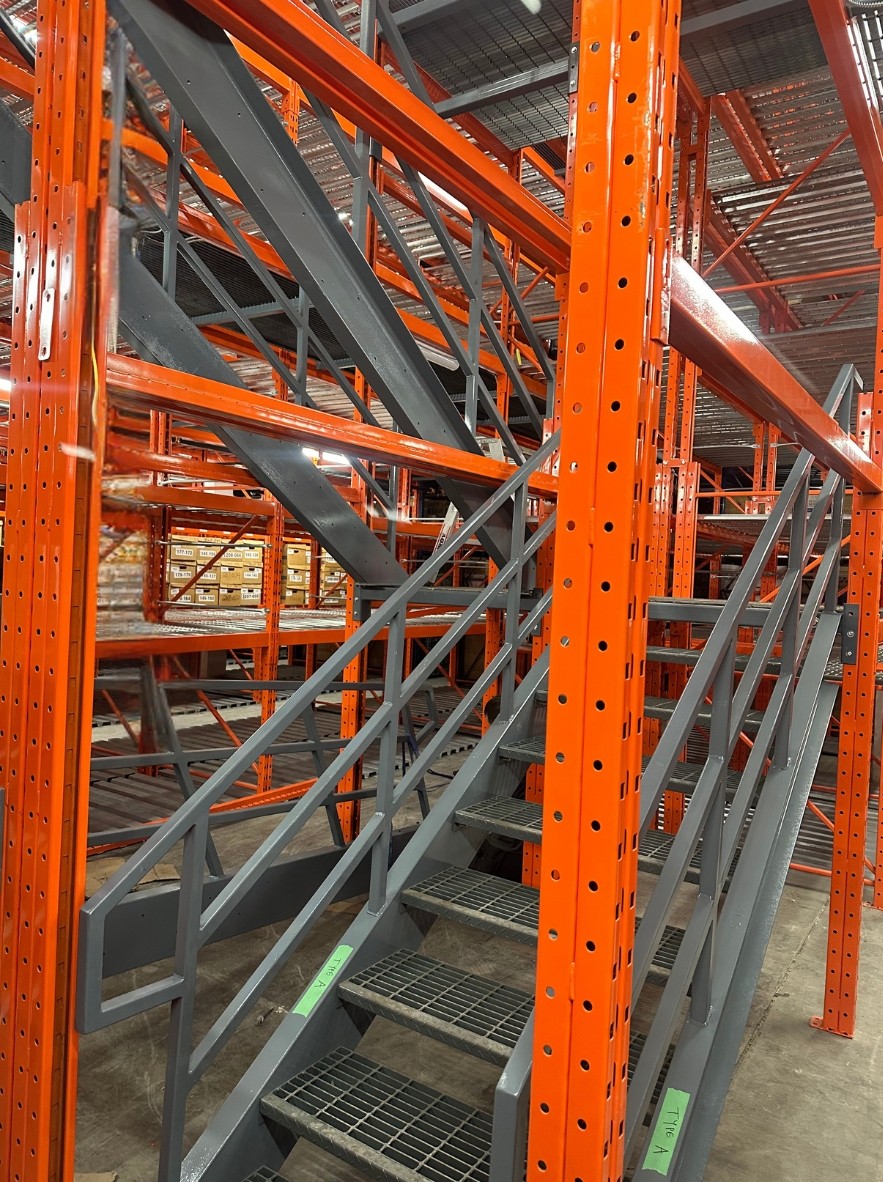
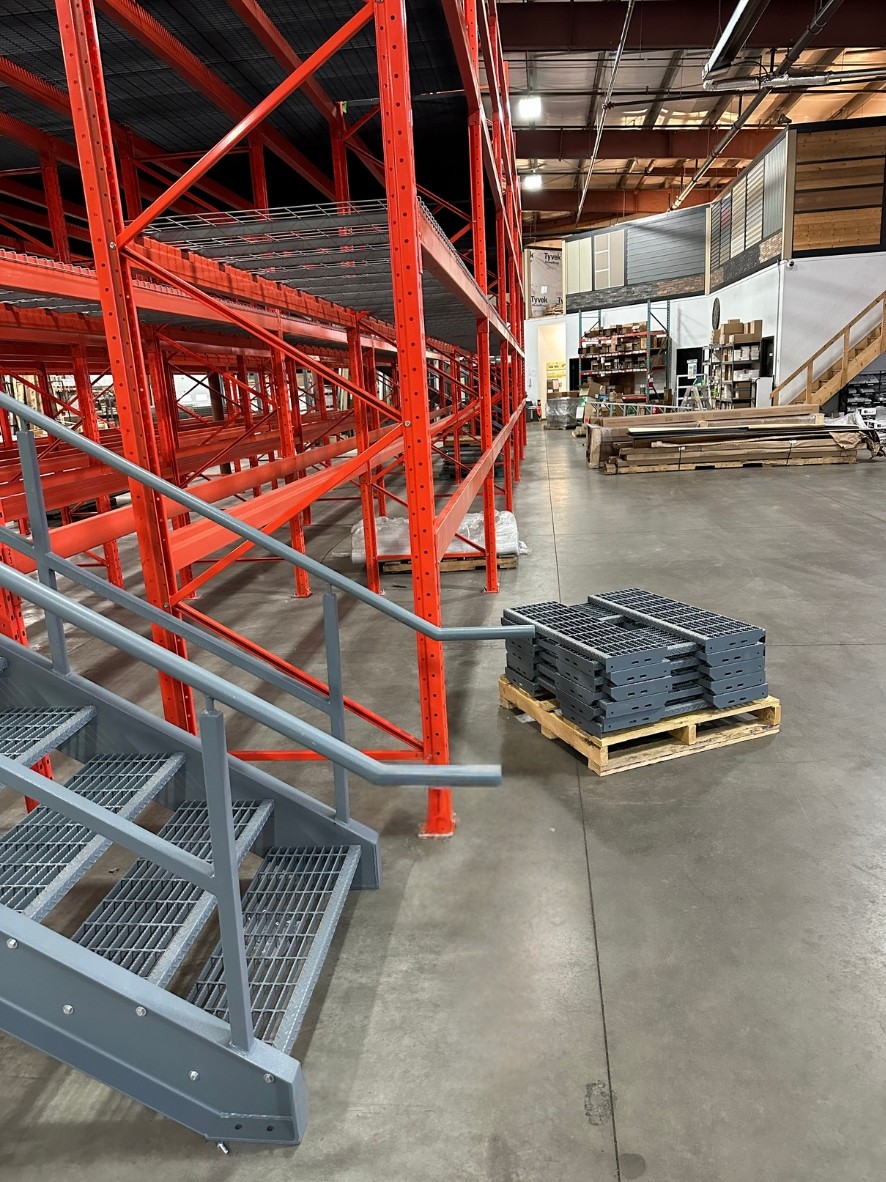
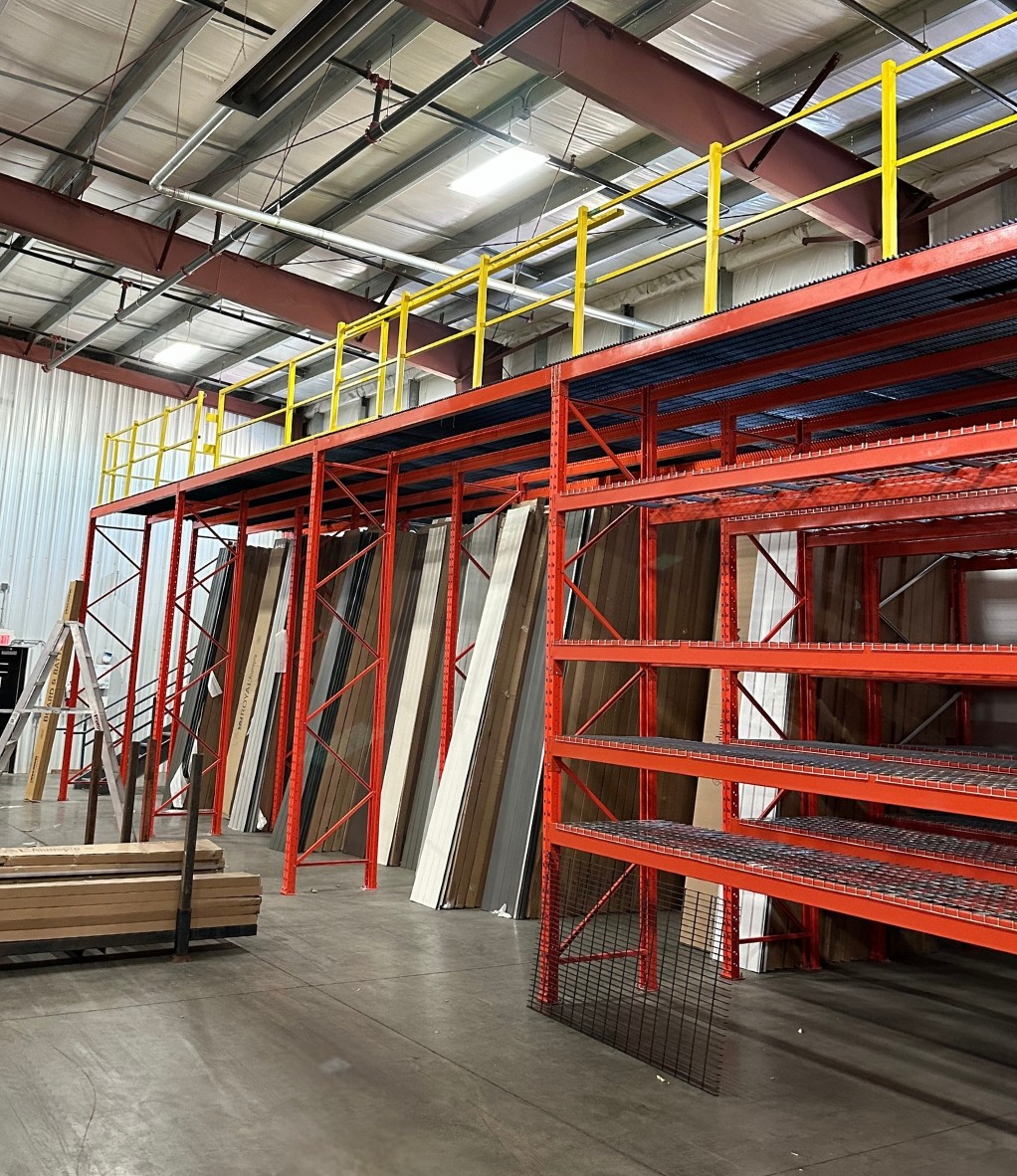
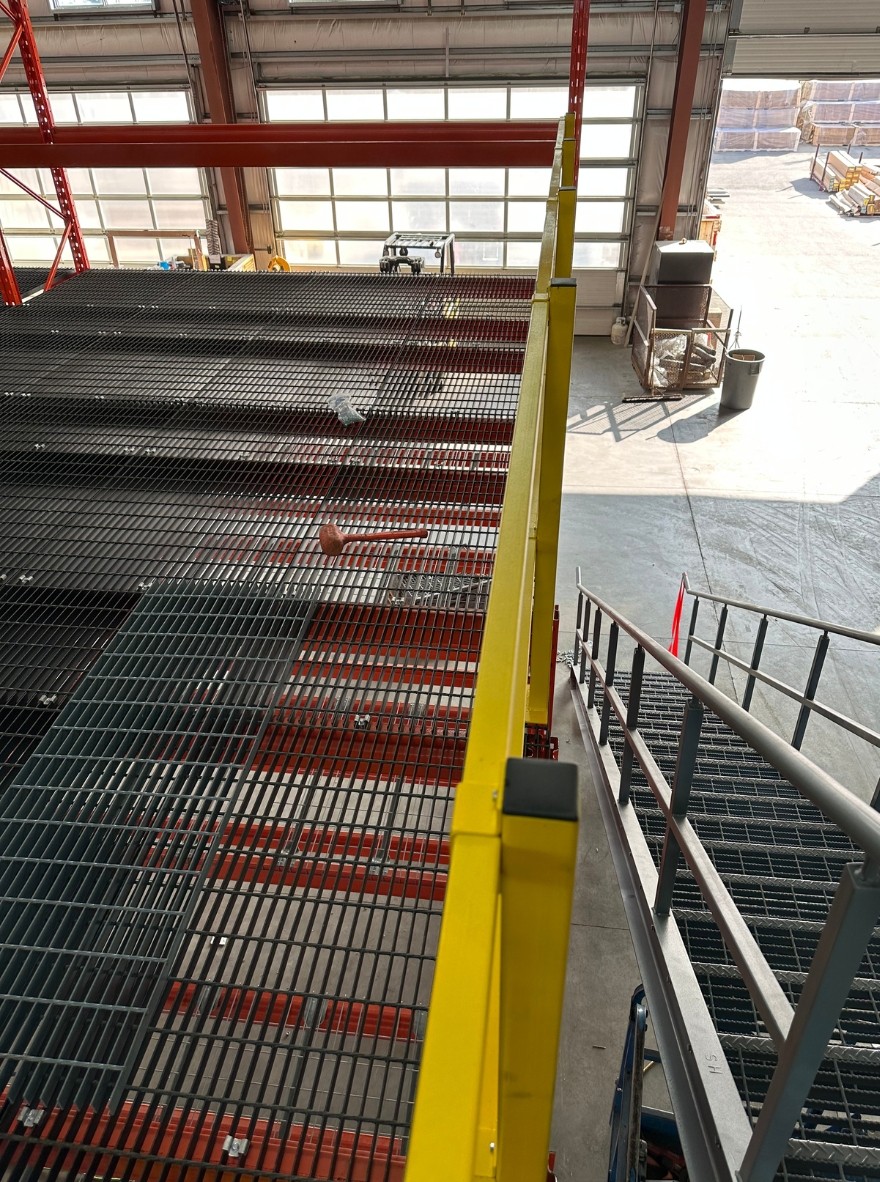
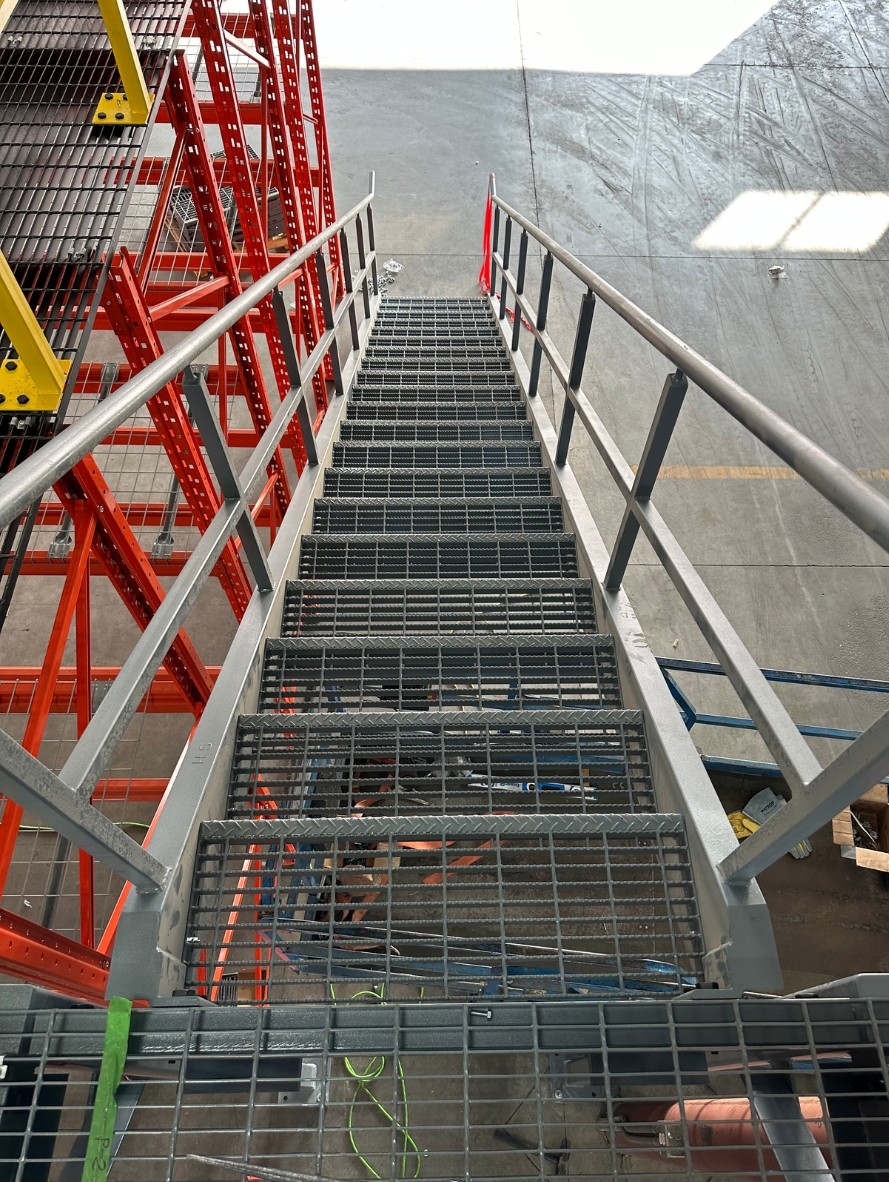